Requirements for Drilling in Rock Drilling and Blasting Operations
Source:
/en Release date: 2024-09-03
Generally speaking, drilling is described by four characteristics: longitude, depth, straightness, and stability.
1. Hole diameter
The diameter of the borehole depends on the purpose of using it. There are many factors that affect the selection of holes in blasting drilling operations.
Generally speaking, drilling is described by four characteristics: longitude, depth, straightness, and stability.
1. Hole diameter
The diameter of the borehole depends on the purpose of using it. There are many factors that affect the selection of holes in blasting drilling operations. For example, the required size of rock particles after rock breaking; The type of blasting selected; The rock particles blasted meet the requirements of "quality" (smoothness of particle surface and proportion of fragmentation); The allowable level of surface vibration during blasting operations. In larger quarries or large open-pit mines, the use of large-diameter blasting operations often reduces the drilling and blasting costs per ton of rock. In underground rock drilling operations, mining equipment is limited by the underground space. In the drilling operation of water wells, the size of the rock hole depends on the diameter of the pipe or the diameter requirements of the supporting equipment required by the water pump. In terms of rock support holes, the diameter of different anchor rods is the determining factor.
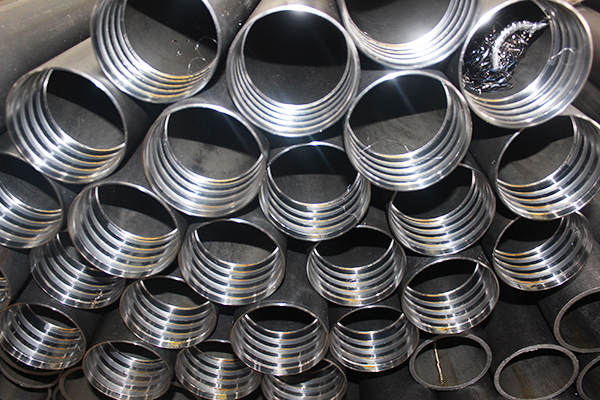
2. Depth of hole
The depth of the hole is affected by the rock drilling equipment, and only short drilling tools can be selected in limited space. Short drills with threaded connections are essential for rock drilling in confined spaces. In the rock drilling operation of blasting rock holes (horizontal or vertical holes), the depth of the drilled hole should be slightly deeper than the theoretical depth or terrace height. In some rock drilling conditions, it is required to drill at a deeper depth (50-70 meters or more), and the down the hole drilling method is generally used instead of the top hammer impact drilling method. The energy transfer and powder discharge effect of the down the hole drilling method are more efficient under deep hole conditions.